PILOT PLANTS
In order encourage entrepreneurship and develop the technically competent manpower for food processing and production of value added products, NIFTEM has setup food processing pilot plants equipped with a range of cutting-edge equipment and food processing / production lines to perform various types of unit operations.
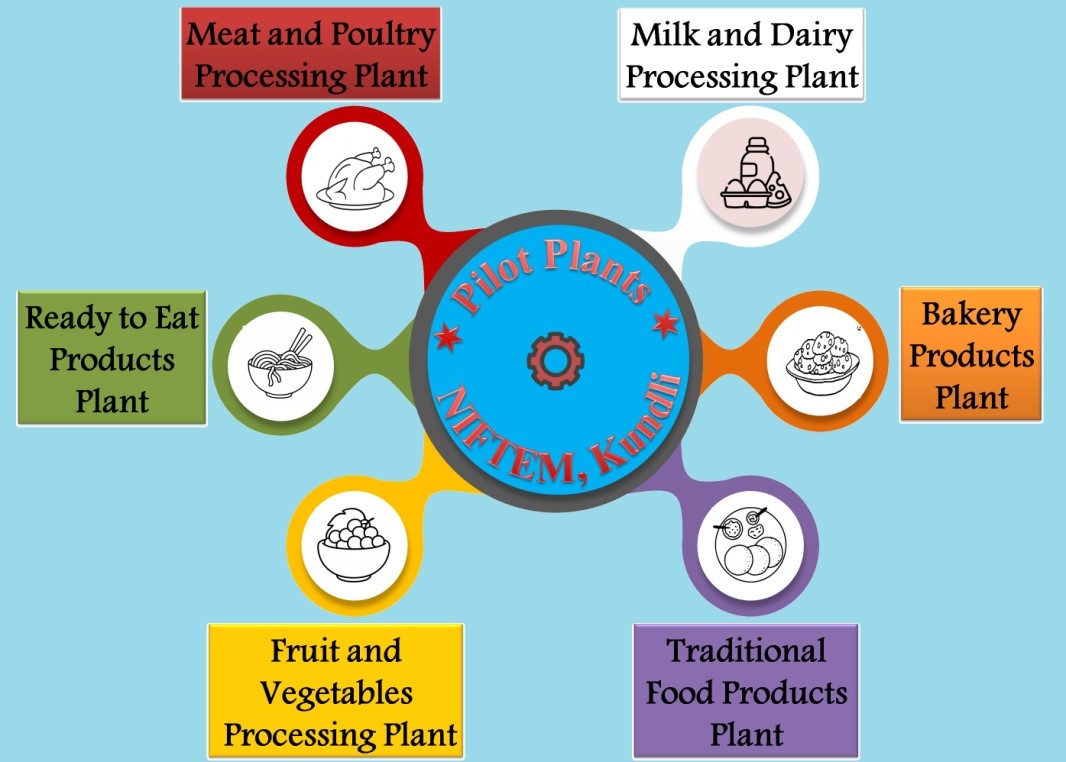
NIFTEM Pilot Plant Central Licensee Download
Services Offered by NIFTEM Pilot Plants
- Business incubation for start-ups and budding entrepreneurs.
- Customized training and demonstrations of equipment operation to potential entrepreneurs.
- Development of new products and processes; and upscaling them to industry level.
- Facilitating production trials for optimization of inputs; product quality; efficient production and assessment of cost.
- Commercial production of food products by incubates and entrepreneurs who are just starting up.
- Identify areas for improvement in output capacity, energy saving, and waste and carbon foot-print reduction in food start-ups and MSMEs, and extend necessary support and guidance.
Production Trials / Development of New Products or Processes
Startups, Entrepreneurs and any Industries interested in production trials / development of novel and innovative products, and upascaling of technologies to industry scale, please write to us, chairmanpilotplants@gmail.com NIFTEM Pilot Plants works out to be economic for optimization of inputs; product quality; efficient production and conducting trials for assessment of cost.
Commercial Production on Monthly License Basis
NIFTEM Pilot Plants facilities are offered on monthly license basis to incubatees and entrepreneurs who are just starting up for commercial production of food products.
Training Programmes
A. Regular Training Programmes
4-weeks Training programmes on Food Technology Entrepreneurship Development are conducted to pre-final year and undergraduate students of Food Technology / Agricultural Engineering or equivalent in June, July and December months. For more information, click here. If similar training programmes needs to be arranged for more than 15 students in other months, please write to us, chairmanpilotplants@gmail.com
B. Customized Training Programmes
SHGs, FPCs, progressive farmers, group of students and any potential entrepreneurs interested in any customized training to develop and strengthen specific skills and abilities in food processing and production of value added products, please write to us, chairmanpilotplants@gmail.com Here is a list of various hands-on trainings on the production of value added products from millets, dairy, fruits and vegetables, mushroom, traditional sweets, snacks and savory foods offered by Pilot Plants. Click here.
Technical Competency Development Programmes
Programmes on operation, adjustments, servicing and maintenance of advanced food processing machines such as IQF, CAS and MAP, Cold storage, Ripening chamber, Spray dryer, Extruders, Dryers and Evaporators for food plant operators and executives.
Technical Gap Analysis and Handholding
We extend support and guidance for process improvements, energy saving, and waste and carbon foot-print reduction in food industries, food start-ups and MSMEs.
We offer guidance on establishment of Food Processing Plants, with utilities and accessories for the efficient production of value added products.
Facilities in Pilot Plants
1. Ready to Eat (RTE) Food Products Pilot Plant
Process Lines
- Twin screw extruded flakes, puffed and core filled products
- Rotary head extruded kurkure type snacks
- Fruits and nuts /cereal / nutri bar
- Burger patty and nugget
List of Equipment
Sl. No. | Equipment | Capacity | |
---|---|---|---|
1. | Air puffing machine | 50-60 kg/h | |
2. | Multi head automatic granules packaging machine | 20 Packets/min | |
3. | Liquid packaging machine | 60 Packets/min | |
Dry Extrusion Products Line |
|||
4. | Ribbon blender | 100-200 kg/h | |
5. | Screw conveyor | 100-200 kg/h | |
6. | Twin screw extruder | 100-200 kg/h | |
7. | Five layer continuous dryer | 100-200 kg/h | |
8. | Cooking machine | 100-200 kg/h | |
9. | Seasoning machine (Double roller flavoring machine with oil/ sugar sprayer)- sugar melter, sugar sprayer, double roller flavor machine | 100-200 kg/h | |
10. | Flaking mill | 100-200 kg/h | |
11. | Essential accessories: multi-functional shaper, core filler, core filling dies (sticks, biscuit, round and square) with die head (doritos, salad, bugles, rice cracker, tangles and different types) | ||
Rotary Head Extruded Kurkure type Snacks Line |
|||
12. | Vertical mixer | 100-200 kg/h | |
13. | Screw conveyor | 100-200 kg/h | |
14. | Rotary head extruder | 100-200 kg/h | |
15. | Tumble sifter | 100-200 kg/h | |
16. | Seasoner (Single roller flavor machine) | 100-200 kg/h | |
Fruits and Nuts /Cereal / Nutri Bar Line |
|||
17. | Sugar boiling pot | 100-150 kg | |
18. | Mixing machine | 100-150 kg/h | |
19. | Ascension conveyor | 100-150 kg/h | |
20. | Automatic cut and form machine | 100-150 kg/h | |
21. | Packaging machine | 100-150 kg/h | |
Burger Patty and Nugget Line |
|||
22. | Burger machine | 100 kg/h | |
23. | Battering machine | 100 kg/h | |
24. | Breading Machine | 100 kg/h | |
25. | Flouring machine | 100 kg/h |
2. Bakery Products Pilot Plant
Process Lines
- Bread / bun / rusk
- Cookies / muffin / puff / pastries / cakes
List of Equipment
Sl. No. | Equipment | Capacity |
---|---|---|
1. | Flour sifter cum siever | 100-200 kg/h |
2. | Spiral mixer with detachable & one extra bowl | 200 kg/h |
3. | Bowl tilter with lifter | 200 kg/h |
4. | Dough divider, dough division range: 100-1000 g | 200-2000 pieces/h |
5. | Bun divider, dough division range: 30-300 g | 600-7000 pieces/h |
6. | Rounder for bread / rusk, dough rounding range: 100-1000 g | 200-2000 pieces/h |
7. | Intermediate proofer | 200-2000 pieces/h |
8. | Dough molder, dough weight range: 100-1000g | 200-2000 pieces/h |
9. | Final proofer, temperature: upto 40⁰C, RH: upto 90% | |
10. | High speed slicer | 200-2000 pieces/h |
11. | Rotary oven with rack, gas and electric, single trolley 25 shelves (50 Tray), Temperature: upto 250⁰C | |
12. | Planetary mixer with batter lifting pump | 150 kg/h |
13. | Cake depositor having 6 dropping points, weight: 50-500 g | 150 kg/h |
14. | Cookies wire cut & dropping machine | 150 kg/h |
15. | Dough sheeter and cutting system, minimum thickness 1 mm | 150 kg/h |
16. | Bread stick machine, Imported / Indian, thickness: 5-30 mm | 25-50 kg/h |
17. | Croissant molding | 2000 pieces/h |
18. | Center filling machine / injector moulding | 25-40 kg/h |
19. | Center filling machine / injector moulding | 5-50 kg/h |
20. | Donut machine with fryer | 440 pieces/h |
21. | Cream cooker | 30 L |
22. | Water chiller, 5000 L | 110 L/h |
23. | Water dozer | 50 L/h |
24. | Walk–in cold room, 2.5 m x 2.5 m x 2.5 m | |
25. | Packaging machine | 30-80 Pouches/min. |
26. | Fully automatic horizontal flow wrap machine | 30-80 Pouches/min. |
3. Fruits and Vegetables Processing Pilot Plant
Process Lines
- Pulps, purees, juices, squash, cordial and formulated beverages
- Jams, jellies and marmalades
- Fruit bars and fruit candy
- Frozen foods
- Concentrates and spray dried products
- Storage and ripening facilities for fruits and vegetables
List of Equipment
# | Equipment | Capacity |
---|---|---|
1. | Steam jacketed boiling pan | 500 L |
2. | Multi effect falling film evaporator | 100 kg/h |
3. | Pulper | 100 kg/h |
4. | Juice extractor | 100-200 kg/h |
5. | Screw press | 100-200 kg/h |
6. | Colloid mill | 100 L/h |
7. | Homogenizer | 200 L/h |
8. | Batch mixing tank | 500 L |
9. | Steam jacketed syrup making tank | 500 L |
10. | Bottle washer | 20 bottles/min. |
11. | Bottle filling machine | 20 bottles/min. |
12. | Coring and peeling machine | 0.3-1.0 MT/h |
13. | Slicing machine | 100 kg/h |
14. | Cubing machine | 100 kg/h |
15. | Bottle capping machine | 10 bottles/min. |
16. | Bottle crimping machine | 10 bottles/min. |
17. | Bottle labeling machine | 20 lables/min. |
18. | Plate and frame filter press | 100 kg/h |
19. | Sparkler filter | 100 L/h |
20. | Plate heat exchanger | 200 L/h |
21. | Autoclaves | 150 kg |
22. | Pouch filler | 10 Pouches/min. (500 mL in each pouch) |
23. | Form-fill-seal machine | 10-20 Pouches/min. (500 mL in each pouch) |
24. | Can reformer | — |
25. | Can filler | 10 Cans/min. |
26. | Can seaming machine | 10 Cans/min |
27. | Conveyor belt | 12 ft length, 2ft width |
28. | Tray dryer | 100 kg/h |
29. | Spray dryer | 65 kg/h |
30. | IQF plant | 100 kg/h |
31. | Plate freezer | 100 kg/h |
32. | Prefab walk in chiller | 2.0 MT |
33. | MA/CA cold storage | 1.0 MT |
34. | Ripening chamber | 550 L |
4. Meat and Poultry Processing Pilot Plant
Process Lines
- Cured meat products
- Comminuted / emulsified meat products
- Coated meat products
- Roasted meat products
- Reconstructed products
- Traditional meat products
Sl. No. | Equipment | Capacity (FG) |
---|---|---|
1. | Automatic mixer grinder/mixer | 75 L/batch (Hopper capacity) |
2. | Hydraulic filler, stuffer (vacuum) | 200 kg/h |
3. | Link cutters | 100 kg/h |
4. | Ham cooker | 35 kg/batch |
5. | Forming line, portioning machine | 100-200 kg/h |
6. | Injector | 500 kg/h for whole bird or big pieces of meat |
7. | Tumbler | 100 kg/batch |
8. | Heavy duty automatic slicer | 100-200 kg/h |
9. | Ice maker | 1500 kg/24 h at ambient condition |
10. | Gas flushing machine | 7-20 trays/min. |
11. | Stewing, cooking range, broiling, frying, roasting machines | 5 kg or L/batch |
12. | Metal detector | 3 feet x 1½ feet tunnel |
13. | Band saw | |
14. | Chiller | 2 MT |
15. | Cold store ( -18°c) | 8 MT |
16. | Blast freezer (-18 to -25°c) | 500 kg/batch |
17. | Bowl cutter | 40 L |
18. | Meat skewer machine | 200 skews/h |
5. Milk and Dairy Products Pilot Plant.
Process Lines
- Liquid milk processing (cream separator, homogenizer and FFS machine)
- Ice-cream production (with automatic cup filling machine)
- Paneer production (with pneumatic press)
- Flavored milk preparation (bottle filling, sterilization)
- Butter production
- Ghee production (with FFS machine)
- Dahi preparation (with automatic cup filling machine)
- Shrikhand preparation
- Membrane filtration unit
List of equipments Available
Sl. No. | Equipment | Capacity |
---|---|---|
Milk Reception Section | ||
1. | Platform type milk weighing machine | 1000 L |
2. | Dump tank- Stainless steel | 1000 L |
3. | Duplex inline filter | 1000 L/h |
4. | Milk chiller (plate type) | 1000 L/h |
5. | Raw milk storage tank | 1000 L |
Milk Processing Section | ||
6. | HTST pasteurizer | 1000 L/h |
7. | Cream separator | 1000 L/h |
8. | Milk homogenizer | 1000 L/h |
9. | Skim milk storage tank | 1000 L |
Cream Processing, Butter and Ghee Section | ||
10. | Cream balance tank | 250 L |
11. | Cream balance tank | 250 L |
12. | Cream chillers | 250 L/h |
13. | Cream ripening tank | 250 L |
14 | Cream ageing tank | 250 L |
15 | Continuous butter making machine | 250 L/h |
16 | Butter melting vat | 250 L |
17 | Butter milk chillers | 250 L/h |
18 | Ghee boiler | 250 L/h |
19 | Ghee strainer with balance tank | 250 L |
20 | Ghee settling tank | 250 L |
21 | Ghee clarifier | 250 L/h |
22 | Ghee granulation tank | 250 L |
23 | Ghee pouch filling machine | 250 L/h |
Milk Poly Pack Section | ||
24 | Milk balance tank with float valve | 500 L |
25 | Milk pouch filling machine | 500 L/h |
Dahi /Chaach /Lassi Section | ||
26 | Curd setting tank | 500 L |
27 | Curd breaker assembly | 500 L/h |
28 | Cup filling & sealing machine | 500 L/h |
29 | Curd incubation room | 500 L |
Paneer / Cheese Section | ||
30 | Paneer / cheese vat | 500 L |
31 | Paneer / cheese washing cum cooling tank | 500 L |
32 | Paneer / cheese press single head | 500 L/h |
33 | Paneer packing with poly liner under vacuum (vacuum pack) | 500 L/h |
34 | Paneer cabinet, vertical cooler (front opening) | 500 L/h |
35 | Separator / basket centrifuge | 500 L/h |
36 | Shrikhand mixing vat | 500 L |
37 | Cup filling & sealing machine | 500 L/h |
Ice Cream Section | ||
38 | Ageing vat | 200 L |
39 | Ice cream mix homogenizer | 200 L/h |
40 | Ice cream mix pasteurizer | 200 L/h |
41 | SS Choco -bar / mango / other flavour tunnel | 200 L/h |
42 | SS Chocó -bar/ mango / other flavour dip tank | 200 L |
43 | SS Lolly pop defrosting tank | 200 L |
44 | Batch freezer | 200 L/h |
45 | Continuous freezer | 200 L/h |
46 | Fruit feeder | 200 L/h |
47 | SS Mix flavouring tank | 200 L |
48 | Cup cum cone filling machine | 200 L/h |
Flavored Milk Section | ||
49 | Multipurpose vat | 250 L |
50 | Sugar mixing tank | 250 L |
51 | Double head filling machine | 250 L/h |
52 | Shrink wrapping machine | 250 L/h |
53 | Bottle sleeving machine | 250 L/h |
54 | Bottle corking machine | 250 L/h |
55 | Ink jet printer | 250 L/h |
56 | Bottle sterilizer | 250 L/h |
Membrane Processing Section | ||
57 | Ultra filtration plant | 100 L flux rate/h |
58 | Microfiltration | 100 L flux rate/h |
59 | Reverse osmosis | 100 L flux rate/h |
60 | Ion exchange plant | 100 L flux rate/h |
CIP Section | ||
61 | Detergent solution tank | 1000 L |
62 | Acid solution tank | 1000 L |
63 | Hot water tank | 1000 L |
64 | Duplex filter | 1000 L/h |
Traditional Food Products Pilot Plant
Sl. No. | Equipment | Capacity |
---|---|---|
1. | Automatic sheeting and die cutting machine | 800-1200 Pieces/h |
2. | Semi-sheeter machine | 50-60 kg/h |
3. | Automatic papad drying machine | 1-15 kg/h |
4. | Auto farsan namkin machine with fryer | 100-200 kg/h |
5. | Batch fryer | 5 L |
6. | Auto peeling machine | 200 kg/h |
7. | Auto chips cutting machine | 200 kg/h |
8. | Auto hydro dryer machine | 200 kg/h |
9. | Atta blending Machine | 10-12 kg/h |
10. | Pulveriser machine for spices | 10-80 kg/h |
11. | Pulveriser machine for flour | 10-40 kg/h |
12. | Auto heating mixing machine | 50 L |
13. | Heavy duty wet grinder | 5 L |
14. | Gravy making machine | 10-150 kg |
15. | Automatic gulla cutting and rounding machine | 2000 Pieces /h |
16. | Automatic laddu making machine | 2000 Pieces /h |
17. | Semi-automatic chakli making machine | 40-80 kg/h |
18. | Dosa making machine | 350-400 Pieces /h |
19. | Vada making machine | 600-800 Pieces /h |
20. | Idly steamer | 100 Pieces/batch |
21. | Hydraulic tablet pressing machine | 1200 Tablets/h |
22. | Pop corn machine with electrical heating system | 250 g/batch |
Cost of Equipment and Processing Lines
For initial cost of equipment and processing lines, please click here. This is presented with a view to estimate the cost of establishing process lines in food processing industries, calculation of the cost of production of processed and value added food products, and assessment of the cost of taking over the machinery on monthly license basis.
For more details, please contact NIFTEM Pilot Plant Committee
All activities and initiatives of the NIFTEM Pilot Plants are implemented through a technical committee, Pilot Plant Committee, comprising of a Chairman and Faculty Incharges of individual pilot plants as members. The Manager (Pilot Plants) executes all the initiatives taken by the NIFTEM Pilot Plants Committee.
Contact Details
# | Name | Detalis |
---|---|---|
1. | Prof. Prassana Kumar G.V. Chairman,NIFTEM Pilot Plant Committee |
Telephone: +91-130-2281043 Mob: +91-8638941500, 9435638360 Email id: chairmanpilotplants@gmail.com Prasanna.niftem@gmail.com |
2. | Aditya Sharma (Manager, NIFTEM Pilot Plant) |
Mob: +91-7015504639 Email id: Aditya.sharma@niftem.ac.in |
3. | Dr. Ankur Ojha Faculty In- Charge RTE & Traditional Food Products Pilot Plant |
Email id: aojha.niftem@gmail.com |
4. | Er. Anand Kishore Faculty In- Charge Bakery Products Pilot Plant |
Email id: anand.iitkgp14@gmail.com |
5. | Dr. Sunil Parik Faculty I/C Fruits and Vegetable Processing Pilot Plant |
Email id: sunilpareek.niftem@gmail.com |
6. | Dr. Prarbdh Badgujar Faculty In- Charge Meat & Poultry Processing Pilot Plant |
Email id: prarabdh.niftem@gmail.com |
7. | Er. Nitin Kumar Faculty In- Charge Milk & Dairy Products Pilot Plant |
Email id: nitinkumar.iit@gmail.com |
Gallery


